By fabmax | 06 September 2024 | 0 Comments
Mastering the Art of Press Brake Tooling for Modern Manufacturing
In the fast-evolving world of manufacturing, precision and efficiency are key. One of the tools that stands out in achieving these goals is the press brake. Specifically, press brake tooling has revolutionized the way we approach bending and shaping metal.
Understanding Press Brake Tooling: Types and Applications
Key Features to Look for in High-Quality Press Brake Tooling
Benefits of Using Standard Punches in Your Manufacturing Process
Future Trends: Innovations in Single V-Die Design and Technology
For many manufacturers, including small-scale operations and large enterprises, understanding press brake tooling can make the difference between average and exceptional production outcomes. This comprehensive guide will walk you through the essentials of press brake tooling, highlight the critical features to look for, and explore future trends that could shape the industry.
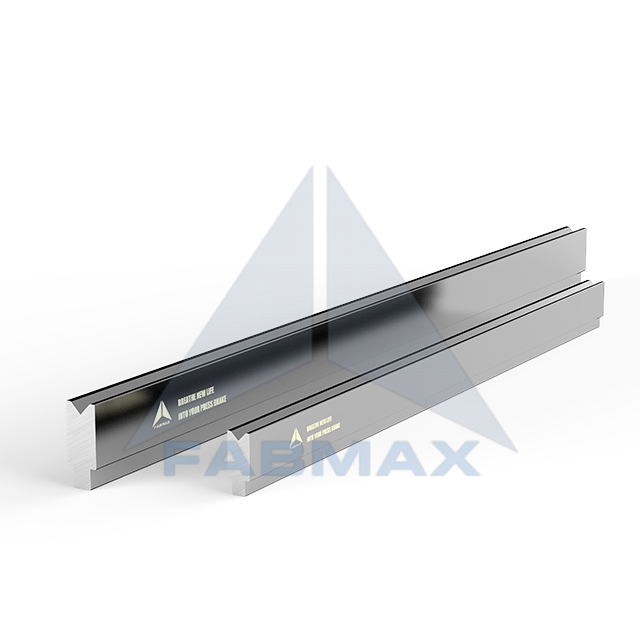
Understanding Press Brake Tooling: Types and Applications
Press brake tooling refers to the various tools and dies used in conjunction with a press brake machine to bend or shape metal sheets. The primary components include punches and dies, which come in various shapes and sizes to cater to different bending requirements. There are multiple types of press brake tooling, including single V-dies, multi-V dies, and specialized tooling for specific applications. Single V-dies are particularly common in CNC press brakes due to their high precision and versatility. They are available in angles of 30 or 88 degrees with V openings ranging from 0.157 inches to 0.984 inches. These tools are essential for creating specific bends and shapes in metal sheets, enabling manufacturers to produce parts with exact dimensions and tight tolerances.Key Features to Look for in High-Quality Press Brake Tooling
When selecting press brake tooling, it's crucial to focus on quality and durability. High-quality tooling not only ensures precise bends but also prolongs the life of your equipment. Look for tooling made from robust materials that can withstand significant stress and wear over time. Steel is a popular choice due to its strength and resilience. Additionally, consider the tooling's versatility; tools that can handle various materials and thicknesses will offer more value. It's also essential to choose tooling that is easily adjustable and compatible with your press brake machine. Features like quick-change mechanisms and modular designs can save time and effort during setup and operation, increasing overall productivity.Benefits of Using Standard Punches in Your Manufacturing Process
Standard punches are a staple in many manufacturing processes due to their reliability and ease of use. These tools are designed to work seamlessly with various press brake machines, making them an ideal choice for both standard and customized applications. One of the main benefits of using standard punches is their consistency. They provide uniform bends and shapes, which is crucial for maintaining quality control in mass production. Additionally, standard punches are often readily available, reducing lead times and ensuring that your manufacturing process remains uninterrupted. By incorporating standard punches into your workflow, you can achieve higher efficiency and better product quality, ultimately leading to increased customer satisfaction.Future Trends: Innovations in Single V-Die Design and Technology
The world of press brake tooling is continuously evolving, with new innovations emerging to address the changing needs of the manufacturing industry. One of the most exciting trends is the development of advanced single V-die designs. These innovations focus on improving precision and reducing setup times, making it easier for manufacturers to achieve consistent results. For instance, some new designs feature interchangeable inserts that allow for quick adjustments without the need for extensive reconfiguration. Additionally, advancements in materials science are leading to the creation of more durable and wear-resistant tooling, which can significantly extend the life of your equipment. By staying up-to-date with these trends, manufacturers can take advantage of the latest technologies to enhance their production capabilities and remain competitive in the market.Press brake tooling is a critical component of modern manufacturing, offering the precision and efficiency needed to produce high-quality metal parts. By understanding the different types of tooling, key features to look for, and the benefits of using standard punches, manufacturers can optimize their processes and achieve better results. Furthermore, staying informed about future trends and innovations in single V-die design and technology can help businesses stay ahead of the curve and maintain a competitive edge. If you're looking to take your manufacturing capabilities to the next level, consider incorporating advanced press brake tooling solutions into your workflow. For personalized advice and expert consultation, reach out to our team at FABMAX and discover how we can help you achieve your production goals.
Leave a Reply
Your email address will not be published.Required fields are marked. *